首页 关于远东 产品目录 销售网络 生产设备 公司资质 技术支持 联系我们
抽油泵(防爆油泵,润滑油泵)标准(全文下载)
1 、主题内容与适用范围 本标准规定了有杆抽油泵的型式、代号、基本参数、技术要求、试验方法和检验规则以及油漆包装等要求。本标准适用于从石油井中抽汲油液的有杆抽油泵 2 、引用标准 GB 4457.3 机械制图字体 GB 197 普通螺纹公差与配合 ( 直径 1 ~ 600mm) GB 1804 公差与配合未注公差尺寸的极限偏差 GB 1031 表面粗糙度参数及其数值 GB 252 轻柴油 GB 7229 抽油杆及其接箍 3 、术语 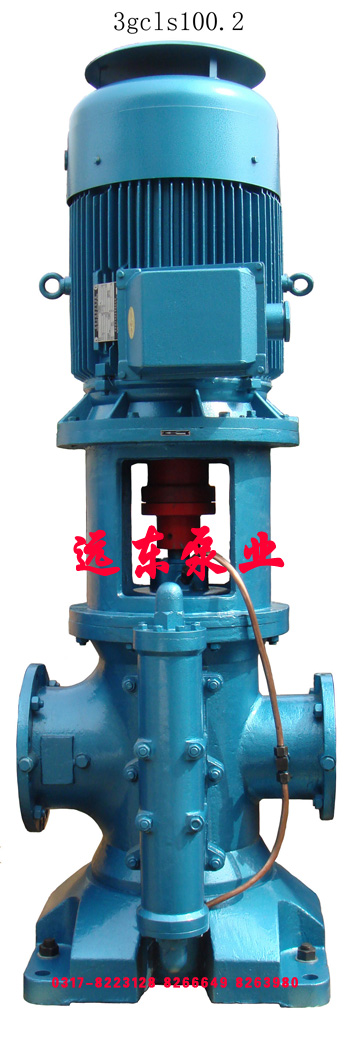 整筒泵(防爆油泵,润滑油泵):无衬套抽油泵。组合泵:有衬套抽油泵。
3 泵常数:某公称直径的泵在一米冲程、每分种一个冲次时的日排量, m/d 。 4 、型式与基本参数 抽油泵的型式与基本参数。抽油泵的型式与基本参数应符合表 1 的规定。 抽油泵的代号及其表示方法。 Ⅱ系列整筒泵的公称直径代号见表 2 。 油管(防爆油泵,润滑油泵)外径及其代号见表 3 。 注:①Ⅰ系列为公制系列,Ⅱ系列为英制换算成公制系列。 ②泵常数供选泵时计算日产量用,方法为:泵常数乘以所需的冲程和冲次。 ③连接抽油杆直径按 GB 7229 规定。 ④加长短节是起调整(弥补)杆管弹性变形量作用的,常规衬套(普通)泵、杆式泵均需要配备加长短节,但是整筒泵一般情况下不需要配备加长短节。 ⑤加长短节是指安装在抽油泵泵筒下接箍与固定阀尔之间的那部分短管。 ⑥至于抽油泵头上部安装的提升短节不能叫做加长短节。表 2
II 系列公称直径 mm | 31.75 | 38.10 | 44.45 | 45.24 | 50.80 | 57.15 | 63.50 | 69.85 | 82.55 | 95.25 | 代号 | 125 | 150 | 175 | 178 | 200 | 225 | 250 | 275 | 325 | 375 |
表 3 油管外径 ,mm | 48.3 | 60.3 | 73.0 | 88.9 | 101.6 | 114.3 | 代号 | 15 | 20 | 25 | 30 | 35 | 40 |
标记示例: 公称直径为 44mm ,泵筒长度为 3m 的厚壁筒,金属柱塞长 1.2m ,顶部机械式固定的杆式泵标记如下: CYB-44RHAM3-1.2 公称直径为 38.1mm ,泵筒长度为 4.5m 的厚壁筒,金属柱塞长 1.5m ,底部机械式固定的杆式泵标记如下: CYB-38RHBM4.5-1.5 公称直径为 70mm ,泵筒长度为 4.5m 的多节衬套式组合泵,金属柱塞长 1.2m ,有一节 0.6m 长的加长短节管式泵标记如下: CYB-70TL4.5-1.2-0.6 备注: API 规范中,薄壁筒壁厚δ =3.175mm ,厚壁筒δ =6.35mm ,中厚壁筒和超厚壁筒的壁厚由生产厂自定,一般中厚壁筒δ =4.763mm ,超厚壁筒δ =8-12mm 5 、技术要求 抽油泵必须符合本标准的要求,并应按照规定程序批准的图样及技术文件制造。 5.2 抽油泵(防爆油泵,润滑油泵)零件所用材料应符合图样规定的材料牌号要求,允许用机械性能和防腐性能 不低于原设计质量要求的其它材料代用,但必须取得制造单位技术部门批准,并办理代用手续。 普通螺纹应按 GB 197 中 6 级精度制造,螺纹的表面粗糙度应符合 GB 1031 规定,其 Ra 值不大于 3.2 μ m 。 图样中 , 未注明尺寸公差的机械加工尺寸应按 GB 1804 规定 , 孔和轴分别按 H14 和 h14 制造 , 长度按 Js15 ( js15 )制造。 零件的配合面、密封面应光洁完整 , 不允许打任何标记 , 衬套内孔和两端面不允许有裂纹、沟槽、划痕等缺陷。 组合泵中的衬套长度应为 300mm 的整数倍。 同一种型式、规格的抽油泵 , 其零件必须能互换。 抽油泵主要零件质量要求。 泵筒和衬套。
5.8.1 .1 整筒泵(防爆油泵,润滑油泵)的泵筒内孔表面和组合泵的衬套内孔表面渗(镀)层厚度、硬度及其基
体心部硬度应符合表 4 的规定。 表 4 内孔镀铬泵筒 , 其镀铬层与基体金属结合应牢固 , 不得有气泡、麻点、起皮或剥落等缺陷。 泵筒内孔表面及衬套内孔表面粗糙度 Ra 值不得大于 0.4 μ m, 衬套两端面粗糙度 Ra 值不得大于 0.8 μ m 。 金属柱塞 金属柱塞表面镀铬、喷焊层厚度和硬度应符合表 5 的规定。表 5 镀铬(喷焊)柱塞,镀层(喷层)应与基体金属牢固结合,其表面不许有气
项目表面处理方法 | 渗 ( 镀 ) 层厚度 ,mm | 表面硬度, HRC | 心部硬度 HB | 镀铬 | ≥ 0.080 或≥ 0.150 加厚 | 66 ∽ 72 | 207~240 | 渗碳或碳氮共渗 | ≥ 0.250 | 58 ∽ 66 | 氮化 | ≥ 0.250 | HV 856 ∽ 1037 |
项目表面处理方法 | 镀 ( 喷 ) 层厚度 ,mm | 表面硬度, HRC | 心部硬度 ,HB | 镀铬 | ≥ 0.100 | ≥ 62 | 207~240 | 喷焊 | ≥ 0.250 | ≥ 53 |
5 泡、麻点、起皮和碰伤等缺陷。 柱塞表面粗糙度 Ra 值不得大于 0.4 μ m 。 泵阀 阀球和阀座的材料和硬度应符合表 6 的规定。 5.8.3 .2 阀球几何精度应符合下列规定: a. 阀球直径公差应为土 0.025mm ; b. 阀球圆度偏差:直径小于 50mm ,则不大于 0.0015 mm ;直径大于或等于 50mm ,则不大于 0.0020 mm ; c. 阀球表面粗糙度 Ra 值应不大于 0.025 μ m. 配合间隙表 6 整筒泵金属柱塞与泵筒的配合间隙分五种 ( 见表 7) 。如果买方合同中未注明间隙
材料 | 3Cr13 | 6Cr18Mo | 9Cr18Mo | 35 铬钨钴合金 | 40 铬钨合金 | 碳化钨合金 | 阀球 | HRC ≥ 51 | — | HRC57~63 | — | HRC56~68 | HRA ≥ 88 | 阀座 | HRC ≥ 48 | HRC52~58 | — | HRC54~61 | — | HRA ≥ 88 |
代号,则制造厂应按 2 号间隙泵供货。表 7 间隙代码 | 泵筒内径及极限偏差 ,mm | | 金属柱塞 | | 泵筒与金属柱塞配合间隙范围, mm | 直径, mm | 尺寸分档 | 极限偏差, mm | 1 | | d-0.025 | 1 | | 0.025~0.088 | 2 | | d-0.050 | 2 | 0 | 0.050~0.113 | 3 | 0.056 0 + - D | d-0.075 | 3 | -0.013 | 0.075~0.138 | 4 | | d-0.100 | 4 | | 0.100~0.163 | 5 | | d-0.125 | 5 | | 0.125~0.188 |
注: D , d 系指公称直径。 5.9.2 组合泵金属柱塞与衬套间的配合间隙分三种(见表 8 ),如果买方合同中未注明间 隙代号,则制造厂应按 1 号间隙泵供货。表 8 间隙代码 | 1 | 2 | 3 | 衬套与金属柱塞配合间隙范围 | 0.02~0.07 | >0.07~0.12 | >0.12~0.17 |
注:按间隙代号称呼泵时,应称做 “ 某号间隙泵 ” 。 5.10 允许制造厂按表 9 中规定的直径尺寸生产组合泵中的衬套和相应柱塞。表 9 衬套内径 | | 金属柱塞直径 | | d | d+0.05 | d+0.10 | | 间隙代码 | D | 1 | — | — | D+0.05 | 2 | 1 | — | D+0.10 | 3 | 2 | 1 |
注: D , d 系指组合泵公称直径。 阀座与阀球接触面的密封必须可靠。 泵组装后,柱塞置于泵筒内,往复拉动和转动时,应轻快灵活,无阻滞。 产品出厂前,所有油管螺纹最终旋紧时应涂上螺纹密封润滑脂。 6 试验方法及检验规则 密封性能试验 阀球与阀座间的密封性能试验 : 将阀球与配研后的阀座置于真空泵吸入口处抽真空,使其真空度达到 85 KPa ( 637 mmHg )后关泵, 5s 内不下降。 6.1.2 泵总成密封性能试验:将组装后的抽油泵(不装柱塞总成) , 上端接试压接头, 另一端为吸入阀,在不低于表 10 中规定的压力下保压 3min ,压力降不得超过 0.5MPa 。表 10 配合间隙漏失量测试:经密封性能试验合格的抽油泵,泵筒内放入选配好的柱塞,一端接上试压接头,另一端旋入专用堵头(若装吸人阀总成时 , 必须使吸入阀打开),置泵于水平位置,在附录 A (参考件)中规定的压力表读数中间值不低于 10MPa 的压力下测漏失量,其漏失量应不超过附录 A (参考件)相应的计算值。 泵筒长度 3m 以上的,测试上、下两个部位,泵筒长度小于或等于 3m 的,只测其下部漏失量。 在测漏失量时,应在压力上升到规定值后保压 3min 再计漏失量。 密封和漏失量试验介质均使用 GB252 中的 10 号轻柴油,在 20 ℃温度时运动粘度为 3 ~ 8mm 2 /S ,柱塞长度为 1.2m 。 试验和检验合格后,应在泵筒内壁和柱塞外表面涂以防锈油,再旋上防护帽。 6.3 每台抽油泵(防爆油泵,润滑油泵)的主要零件,泵筒和金属柱塞的制造工艺方法用工艺特征代号 ( 见表 11) 表示,并打印在泵简上接箍的搬手槽上或铣个槽打印上,顺序见本标准 7.3 条规定。表 11 每台抽油泵必须有制造厂质量检验部门签发的合格证方能出厂。 6.5 产品合格证内容: a. 产品名称及型号; b. 抽油泵公称直径; c. 间隙代号; d. 出厂编号及年月; e. 检验人员签字。
公称直径 | Ⅰ系列 | 32 | 38 | 44 | — | — | 56 | 63 | 70 | 83 | 95 | mm | Ⅱ系列 | 31.8 | 38.1 | 44.5 | 45.2 | 50.8 | 57.2 | 63.5 | 69.9 | 82.6 | 95.3 | 抽油泵型式 | 杆式泵 | 试验压力 MPa | 30 | 28 | 23 | — | 20 | 18 | 16 | — | — | — | 管式泵 | 30 | 28 | 23 | 23 | — | 18 | — | 16 | 12 | 12 |
项目 | | | 代号 | | | 渗碳 | 氮化 | 碳氮共渗 | 镀铬 | 喷焊 | 泵筒 | C | N | CN | Cr | — | 金属柱塞 | — | — | — | | P |
油漆、标志及包装 经检验合格的抽油泵,所有外露非加工表面应喷涂防锈底漆,再喷涂醇酸磁漆或硝基磁漆,漆层应均匀、牢固、不得有皱皮、堆积、斑点、气泡、剥落等缺陷。 抽油泵外露的加工表面,必须进行防锈处理,接箍内、外螺纹应旋紧护帽。 抽油泵标牌内容 7.3.1 每台抽油泵外表面应有出厂标牌,其内容包括: a .制造厂商标; b .抽油泵代号及公称直径; c .制造厂名称; d .制造年月。 7.3.2 在抽油泵上部接箍外表面的规定位置上打上钢印标志,其内容包括: a .制造厂厂标; b .公称直径; c .出厂编号; d .工艺特征代号。钢印标记的字体应按 GB 4457.3 中的 7 号字打印。 7.4 抽油泵出厂时,应用足够牢固并有防潮设施的包装箱。装箱时,零件在箱内应可靠 固定,不得碰撞,备用件应涂以防锈油脂,用油纸或塑料薄膜包装好后装入箱内。 7.5 包装箱外面明显位置上应标明: a. 到站; b. 收货单位名称; c. 发货站; d. 制造厂名称; e. 净质量; f. 毛质量; g. 包装箱尺寸(长×宽×高), m 。 h. 产品名称及型号规格; i. 数量及出厂日期; j. 应在包装箱适当位置上标注 “ 轻放 ” 、 “ 防潮 ” 等字样,字迹要清楚、整齐、美观。 7.6 随机文件应封存在塑料袋里,和附件一起包装入箱。随机文件有: a. 交货清单和装箱单; b. 产品质量证明书(或合格证); c. 产品使用说明书(可每箱一份)。 表 A1 公称直径( mm ) ( Ⅰ系列整筒泵 ) | 试验压力 (MPa) | 间隙代号 | 1 | 2 | 3 | 4 | 5 | 最大漏失量 (mL/min) | 32 | 10 | 200 | 420 | 760 | 1255 | 1920 | 38 | 235 | 495 | 905 | 1490 | 2280 | 44 | 270 | 575 | 1050 | 1725 | 2640 | 56 | 350 | 730 | 1335 | 2200 | 3370 | 63 | 390 | 820 | 1500 | 2465 | 3780 | 70 | 550 | 1170 | 2140 | 3530 | 5420 | 83 | 650 | 1390 | 2540 | 4190 | 6420 | 95 | 750 | 1590 | 2910 | 4790 | 7350 |
表 A2 公称直径( mm ) ( Ⅱ系列整筒泵 ) | 试验压力 (MPa) | 间隙代号 | 1 | 2 | 3 | 4 | 5 | 最大漏失量 (mL/min) | 31.8 | 10 | 200 | 415 | 760 | 1245 | 1910 | 38.1 | 235 | 500 | 910 | 1495 | 2290 | 44.5 | 275 | 580 | 1060 | 1745 | 2670 | 45.2 | 280 | 590 | 1075 | 1770 | 2715 | 50.8 | 315 | 665 | 1210 | 1990 | 3050 | 57.2 | 355 | 745 | 1360 | 2240 | 3435 | 63.5 | 390 | 830 | 1510 | 2490 | 3810 | 69.9 | 550 | 1170 | 2140 | 3530 | 5410 | 82.6 | 650 | 1380 | 2530 | 4170 | 6390 | 95.3 | 750 | 1600 | 2920 | 4810 | 7380 |
表 A3 公称直径( mm ) ( Ⅰ系列组合泵 ) | 试验压力 (MPa) | 间隙代号 | 1 | 2 | 3 | 最大漏失量 (ml/min) | 32 | 10 | 100 | 500 | 1420 | 38 | 120 | 595 | 1690 | 44 | 140 | 690 | 1955 | 56 | 175 | 875 | 2499 | 63 | 200 | 985 | 2800 | 70 | 280 | 1410 | 4010 | 83 | 330 | 1670 | 4750 | 95 | 380 | 1910 | 5440 |
附加说明:本标准由全国石油钻采设备和工具标准化技术委员会提出并归口。本标准由机械电子工业部兰州石油机械研究所、玉门石油管理局总机厂负责起草。本标准主要起草人汤洁玲、高景耀、卿尚玉。本标准参照美国石油学会 APISpec11AX 《抽油泵及其组件规范》( 1989 年 6 月第 9 版)及 API RP 11AR 《抽油泵的维护与使用推荐做法》( 1989 年 6 月第 3 版)。本标准实施之日起 JB 2714-80 , SY 5059 — 85 作废。
上一篇 下一篇 |